BEER
Sustainably produce beer through effective energy management
Better for you, your customers
and the environment
-
Improve energy efficiency
Design an optimal energy supply system that accurately grasps the heat used in manufacturing processes
-
Reduce CO2 emissions
Utilize a heat pump and reuse of steam
-
Reduce production costs
Lean utility facilities and efficient operations
Sustainable beer production
The beer production process uses large amounts of energy for cooling and heating, we believe there is still room to further reduce energy costs and CO2 emissions in order to contribute to a sustainable society. As a manufacturer that is also engaged in thermal engineering, Mayekawa, in addition to developing and providing highly efficient equipment, can also fully ascertain the total amount of energy used in the manufacturing process and design optimal energy supply systems for the production processes and facilities accordingly. Additionally, during operations, Mayekawa service technicians working around the world can share facility operational status, ensuring opportunities for further energy savings are never missed.
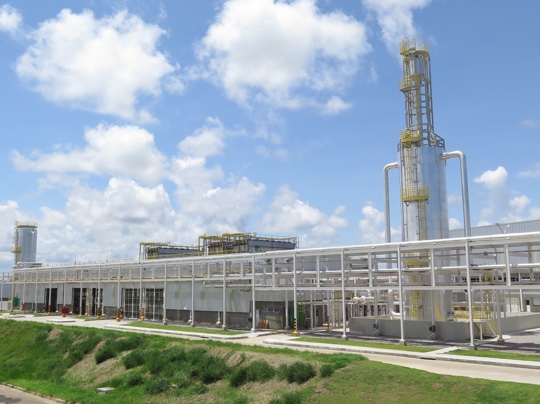
Large temperature difference cooling for brewing water and deaerated water
By employing multistage cooling (cascade cooling) that uses multiple refrigeration stages in the process of cooling the large temperature differences in the cooling of the brewing water and deaerated water, power consumption can be reduced by 20 to 30%. Each refrigeration stage operates within an evaporation pressure that matches the required temperature, resulting in high performance.
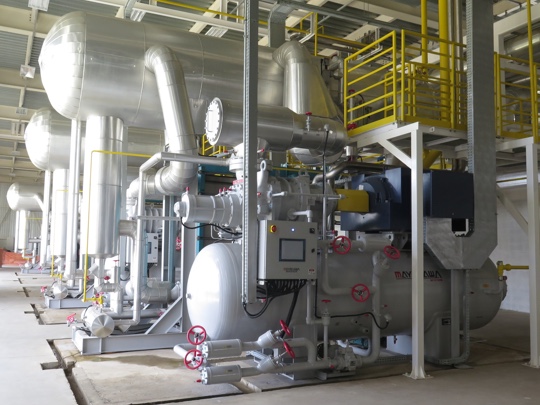
Optimization of fermentation and maturation cooling processes
We recommend indirect cooling using glycol. By utilizing a cylindrical, vertical-type, thermal stratification glycol buffer tank, load fluctuations in the fermentation and aging processes are absorbed. Additionally, the power consumption of the refrigeration system is reduced by shortening low-load operations and constantly operating in a highly efficient manner. As the tank is a vertical cylindrical, type, the power needed for the glycol pump is also reduced.
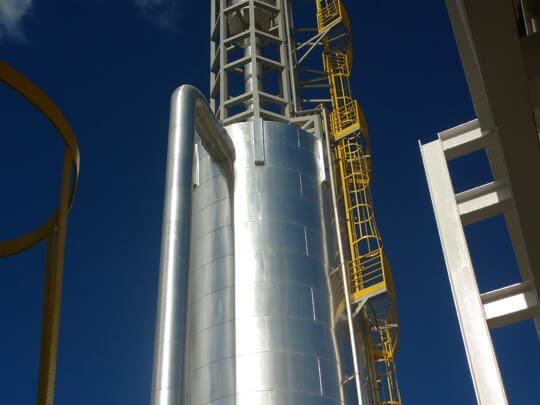
Heat pump for pasteurization
A heat pump is used to supply the hot water that has been pasteurized via a tunnel pasteurizer that is indispensable in the bottling process. By switching the heat source from a steam boiler powered by conventional fossil fuels to a heat pump, CO2 emissions can be significantly reduced. Additionally, there is another model that extracts cold water at the same time, which can then be used for further cooling with the pasteruizer or for other processes.
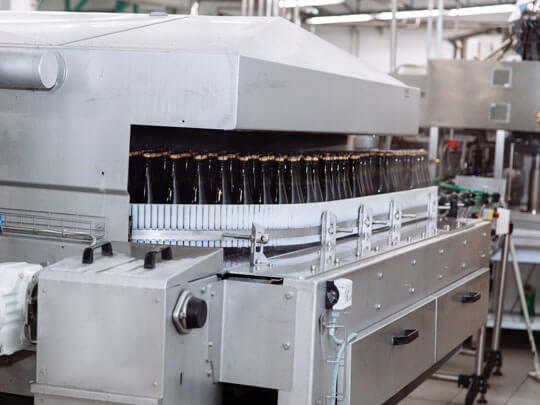