Stories
Collaboration between Mayekawa and a contractor supports seafood processing on the Kamchatka Peninsula
In Russia, on the eastern part of the Kamchatka Peninsula facing the Bearing Sea, vast fields along the shoreline stretch out with no end in sight. In this desolate wilderness far from any populated town, a Kamchatka seafood products manufacturer has set up a salmon processing plant.
The plant started operations in 2018. It processes 100 to 400 tonnes of salmon a day for about three months around June to August when salmon are caught, and then sits idle for the remaining nine months waiting for the next fishing season. The salmon landed here are processed into fillets, frozen, and sent to a cold storage in Vladivostok for distribution to Moscow and China.
Four Thermo-Jack freezers, screw compressor units that supply refrigerant to freezers, and reciprocating compressor units for cold storage use are the Mayekawa products operating at this plant. The freezers were shipped from Mayekawa Japan, while the compressor units are from Mayekawa Russia.
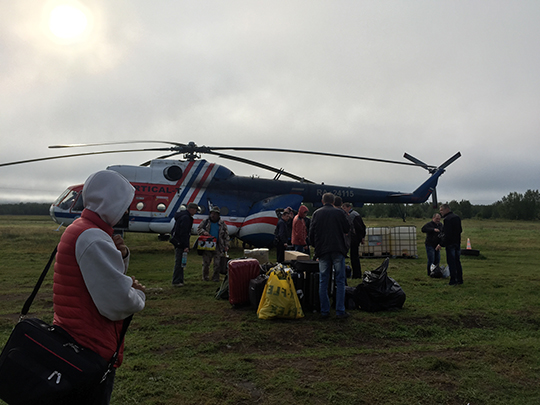
A helicopter used for transportation to the construction site of the new plant
A planned construction site in a vast wilderness location not easily accessible to people
The place where the client set up a new processing plant was in a vast wilderness area far from human habitation. There are no roads to the site, so it is not possible to reach there by car. It is necessary to travel by night bus from Kamchatka a heliport located eight hours away. From there, a further one-hour flight by helicopter is needed.
To purchase the freezers it would use, the client had called upon several different companies. However, the proposals received from companies outside of Russia were limited to just selling the freezers; they would not transport them to the site. This condition presented a significant burden to the client.
The planned site for the new plant was not easily accessible, and it was envisioned that considerable effort would be needed just to bring the actual equipment to the required location. Additionally, when it came to further construction, additional burden would be placed on the companies from outside of Russia, making it difficult for a deal to be struck.
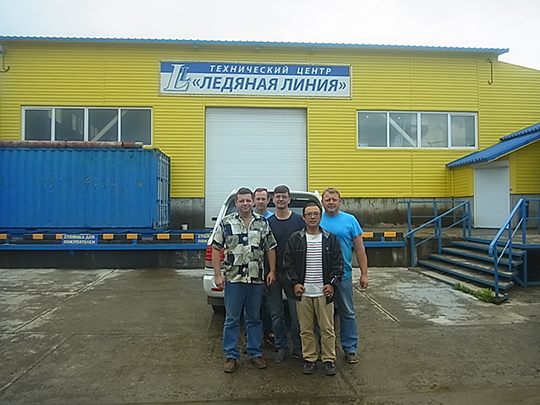
The contractor and team members from Mayekawa visiting an existing plant.
A deep, mutually built relationship of trust led to acceptance
Since 2004, the Kamchatka-based contractor who participated in bidding on the project had been developing a solid relationship with Mayekawa Russia LLC., Mayekawa’s Russian subsidiary. Jointly, they had installed about 120 compressors for refrigeration plants in the Kamchatka area. The contractor who had been contacted by the client for this project did not handle freezers themselves, so they consulted with Mayekawa Russia. Mayekawa manufactures and sells freezers and is expanding globally. However, at that time, Mayekawa Russia had yet to sell freezers to Russia.
Receiving a request to collaborate on the project from the contractor and Mayekawa Russia, Mayekawa dispatched a freezer specialist from Japan to Russia. In August 2016, the specialist visited one of the client’s existing plants together with the contractor and local staff of Mayekawa Russia.
Through information received in advance, it had been learned that two tunnel-type freezers were planned for the new plant. However, it turned out that the client was also considering the introduction of batch freezers. After once more confirming client’s production plan and taking into consideration processing volume, it was determined that it would be more efficient to install continuous freezers over batch types, and the freezers were selected on the spot. After checking the plant blueprints and confirming how much space could be secured, a proposal to install four freezers was ultimately made.
The joint proposal made by the contractor and Mayekawa included onsite construction that was missing from the proposals by other companies. Furthermore, after installation, the contractor and Mayekawa would continue to be involved in equipment maintenance. The client had already built a relationship with the contractor some time ago, and felt, “I will feel even more secure if this contractor also looks after us after the installation has been completed.” Thus, a decision to purchase Mayekawa freezers was made.
Additionally, multiple Mayekawa compressor units had already been installed at the client’s existing factories, which also turned out to be a deciding factor. The client had not experienced any trouble with the equipment operating stably at its existing facilities and thus gave MYCOM compressor high marks. Consequently, they also believed that the freezers would be more efficient and reliable if they were manufactured by Mayekawa as well.
*1: MYCOM is the brand name of Mayekawa’s compressors.
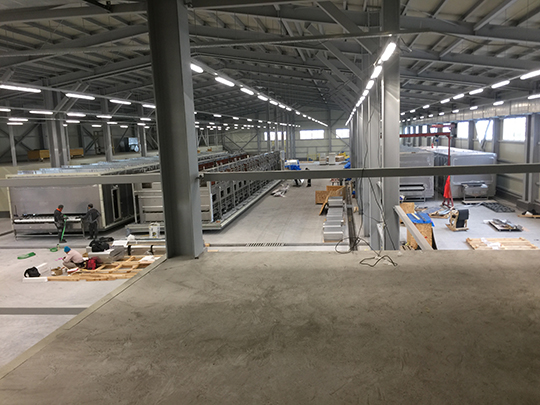
The freezers being installed
Running properly in an isolated location
At the end of August 2017, installation work on the four freezers, the first for Mayekawa to install in Russia, began. Installation was carried out jointly by the contractor and Mayekawa.
Due to bad weather, the helicopter was not operating so it took four nights and five days for the team members involved in the installation to reach the site. Additionally, the site was out of range of cellular service, so the only way to communicate with the outside was through LAN and a telephone line in the client’s office, but these were unstable.
Typically, during installation, if the team wants to confirm something with the Moriya Plant in Japan where the freezers are made, they can make a quick call to solve the problem. At this site, however, it was not that easy.
So, with the client’s cooperation, it was decided that the team would borrow the LAN in the client’s office and communicate via email once a day. Initially, the Mayekawa supervisor was also surprised that communication system was quite limited. However, after about a week, he quickly adapted his thinking, “If I cannot connect normally, I had just better think of another way.”
As people could not easily go back to town, the client had prepared accommodation near the site consisting of shipping containers that had refurbished interiors so people could live in them. In addition to individual rooms for team members involved in the plant construction, a sauna, and a dining hall providing three hot, home-cooked meals a day had also been set up in this residential area. The menu had also been designed to ensure all companies involved in the construction would not grow bored with it.
Though the communication environment was initially unstable, midway through construction, the client brought in Wi-Fi allowing the concerned companies to complete their work without the stress of not being able to communicate normally with the outside world.
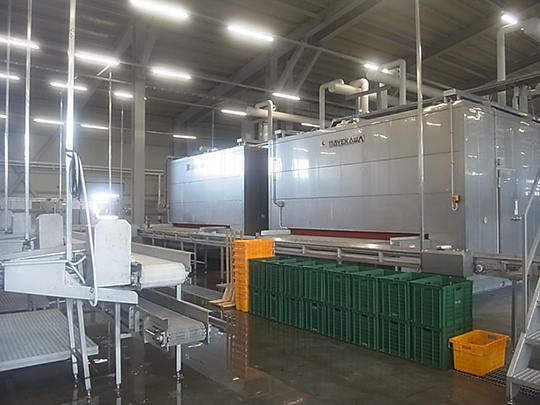
Completed installation of two Mayekawa freezers. Sitting beside these are two more.
Since all the contractor’s staff involved in the installation were competent people, work was able to proceed promptly under the guidance of the supervisor. The installation was initially scheduled to start on August 30 and be completed on October 15. However, on October 4, those involved in the installation work were able to leave the site, having completed construction 11 days early.
At this point, electricity had not yet been connected to the site, so commissioning was temporarily halted. In November, the site was connected to the power grid, and designer of the installed freezers and electricians checked the equipment’s operation, and the plant went into full operation in May 2018.
The client was delighted with the work, and after the plant began full-fledged operations, they ordered an additional freezer from Mayekawa. All five freezers, the initially installed four units plus the additional unit, have been operating properly since the start of full operations up to this present day.
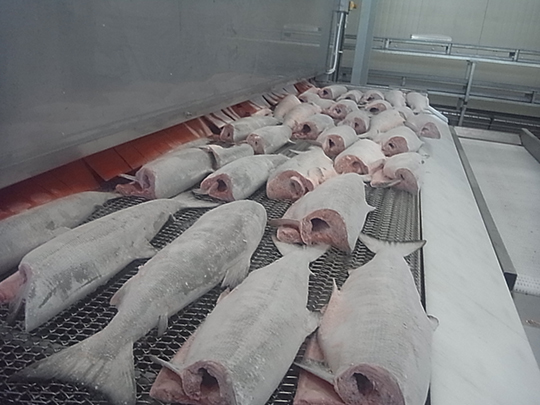
Frozen salmon in a Mayekawa freezer
After the installation, the client provided feedback on three points they were particularly pleased with. The first was improved productivity. Compared to the conventional contact freezers and batch freezers the client was using at existing plants, the Mayekawa freezer was able to freeze product about twice as fast. The second was an improvement in product quality. Thanks to quick freezing capabilities, a feature of Mayekawa freezers, moisture dripping from the salmon could be reduced, allowing it to be frozen without drying too much. Thus, the client was able to produce higher quality salmon than before. The third point was the realization of labor savings. Using conventional contact freezers, the client needed between 12 to 16 employees for operations (1 tonne of processing X 2 lines). By installing the Mayekawa continuous freezers, however, the company could run the process (1.5 tonnes of processing X 2 lines) with just four employees.
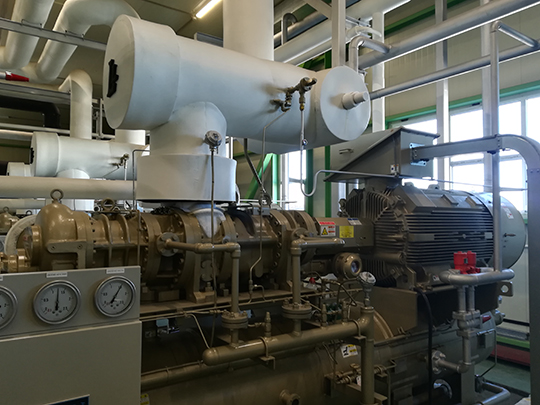
The screw compressor unit suppling refrigerant for the freezer
Trust in Russia is growing for Mayekawa freezers
Mayekawa’s first freezer in Russia started garnering attention from within the country, and another seafood products manufacturer that heard about the story of the Kamchatka site decided to purchase a Mayekawa freezer before completion of construction. Since these first freezers received high marks from clients and have been operating without any troubles thus far, the contractor has started to actively propose Mayekawa freezers to other end-users in the Kamchatka area. Furthermore, at the contractor’s request, Mayekawa began to dispatch freezer specialists to Kamchatka on a regular basis to make proposals to prospective clients together with the contractor. As a result, ten Mayekawa freezers are now operating in the Kamchatka area.
Over the past three years, the contractor has accumulated experience installing Mayekawa freezers jointly with Mayekawa and has thus acquired the technical expertise needed to perform the installation work independently. Regarding maintenance as well, efforts are underway to improve the technical level of the contractor staff, and initiatives such as having them visit the Moriya Plant for training are ongoing. Additionally, it has been decided that technicians from Japan will visit the Kamchatka area later this year and provide more specific guidance and training onsite. The planned outcome for this is to ensure the contractor can respond independently when there is a request for maintenance. If this can be effectively realized, it will bring further peace of mind to end-users.
Freezers are still being installed in the Kamchatka area today, with some clients scheduled to start production in the near future. Going forward, Mayekawa intends to continue building and maintaining a close relationship with end-users in alliance with the contractor and making further proposals for it continues freezers in the Russian Far East.
Our mission is to create a sustainable future by pursuing optimal systems,
equipment and technology while working
side-by-side with customers.