Stories
Supporting local industry today and tomorrow; working closely with clients and communities
Headquartered in Japan, Mayekawa has branches and offices in approximately 60 locations across the country, and those locations are not limited to major metropolitan areas, which are centers of economic activity. Since its early days, Mayekawa has also proactively established bases of operation in more rural areas where local industries prosper. One of those locations is Hachinohe City in Aomori Prefecture, which is located in northern Japan.
Blessed with a rich marine environment that includes the Sea of Japan and the North Pacific Ocean , Hachinohe City lands the largest volume of freshly caught squid in Japan. The seas off its coast are also well-known fishing grounds for mackerel and are the source of fish sold under the valuable and loved Hachinohe-mae-oki mackerel brand. Large catches of fish are brought into the city’s port every day, and the area also prospers as a result of a vibrant processed marine products industry that utilizes those fish as raw ingredients. One company contributing to this prosperity is Maruyo Seafoods Co., Ltd., which has a plant situated on a noticeably large plot in the Kikyono Industrial Park located in the lands back of Hachinohe Port.
The plant was originally built to simply store mackerel, the raw ingredient for shime saba (Japanese marinated mackerel), and squid for overnight drying. However, currently, it is also involved in various processing operations as well.
For a company that needs to secure one years’ worth of raw materials in the short mackerel fishing season, which is currently about three months—September to November—but keeps getting shorter each year, freezers for maintaining the freshness of the mackerel, the raw material for the processed foods and the processed foods themselves, are essential. At present, the plant’s total freezing capacity is 540 tons, one of the largest in all of Japan.
And, for 30 years, Mayekawa has been closely involved in the process of seeing this facility grow into one of Japan’s largest in terms of freezing capacity.
Problems and anxiety caused by changes in the support environment after equipment was initially installed
Mayekawa was not the company initially contracted to build and install the 180-ton freezer that the Kikyono plant started operations with in 1985. However, about 20 years later, when a plan to increase freezer capacity was drawn up, it was Mayekawa who undertook the work.
When adding equipment to an existing facility, it is often preferable to use the manufacturer of the equipment currently in use to help ensure a proper balance and compatibility between the old and new installations. However, for the Kikyono plant, that was not possible, because the manufacturer who was contracted 20 years had closed its offices in Hachinohe City, and the person originally in charge had relocated elsewhere.
This kind of problem is not limited to Japan; it occurs all over the world.Manufacturers often maintain bases in major metropolitan areas. When trouble occurs in areas where they do not receive regular orders or requests for maintenance, they usually dispatch staff from the nearest office to go deal with it. This kind of support structure is still often seen today. While this is reasonable from labor cost and efficiency perspectives, conversely, as there is no one regularly visiting the facility, the manufacturer cannot immediately grasp the circumstances or problems when onsite troubles or requests for consultation occur. This makes it difficult to expediently deal with the situation.
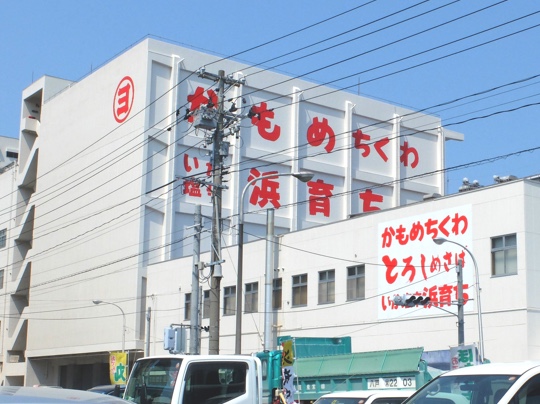
Proposing the best solution while envisioning the future
In the case of them, with the original manufacturer of the freezers having withdrawn from the local area, an environment conducive to ongoing support and maintenance for the equipment installed at its Kikyono plant was lost. During that time, it was the team from Mayekawa’s Hachinohe office who provided equipment maintenance and parts support to the extent possible while visiting the plant to service Mayekawa’s own machinery that had been installed there.
Furthermore, at that time, Mayekawa had installed and was servicing freezers specially designed for freezing squid at the Kikyono plant, not compressors for cooling. In other words, while providing maintenance for its own equipment, it was also servicing cooling equipment that was made by another manufacturer. The reason for this was simple. Regardless of who made the equipment, if it stopped working, the client would be in trouble.
Since its founding, Mayekawa has always considered the client’s position and feelings and worked closely together with them to solve any problems. This is something the company views as being the natural thing to do. It is Mayekawa’s style to always work alongside its clients to help them grow their businesses.
A few years later, when the Kikyono plant freezer expansion plan was raised, the person in charge from Mayekawa was fully committed to one particular aspect, natural refrigerants. While most competitors recommended low-cost and easy-to-use CFC refrigeration units, which were mainstream in Japan at the time, the Mayekawa representative stubbornly pushed for a system that used natural refrigerants.
“Why are you so adamant about this?” When repeatedly asked this, the person in charge stated that while it is true fluorocarbon refrigerants are highly efficient, when coming technological innovation and environmental aspects are considered, they have no future benefit. Moreover, he noted, in addition to simply expanding the plant to increase productivity, having a company that represents the local community set precedent would lead to further development and environmental conservation for the entire region itself. By making a decision in anticipation of this, Their foresight would also be highly appraised.
In other words, Mayekawa not only considers immediate aspects, but also takes into consideration future scenarios and makes proposals based on the way things really should be.
Supplying and servicing local industries while staying close to the community
Since then, They and Mayekawa have worked cooperatively in expanding the scale of the plant. In 2009, They took delivery of four natural refrigerant refrigerators, and in 2013 added two highly efficient NewTon natural refrigerant cooling systems. Over 30 years, Their freezing capacity has grown to become one of the largest in Japan as the company continues to support the fishery industry of Hachinohe City.
During the Great East Japan Earthquake that struck on March 11, 2011, Their headquarters factory in Hachinohe City suffered damage caused by the resulting tsunami. With the help of local contractors such as Mayekawa, however, the facility was quickly restored and put back into operation.
While processed marine products businesses along the Sanriku coast (northeastern Honshu, Japan’s main island) were devasted, operators in the Hachinohe region came together as one to keep supplying marine products to consumers, thus supporting the supply of fishery products across all of northeastern Japan.
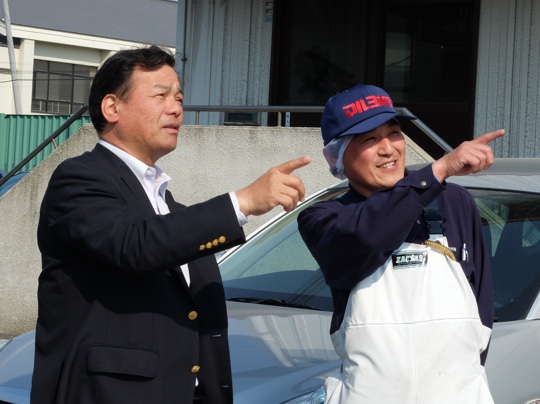
Creating a prosperous future by ensuring stable operations and reliable support
Implementing temporary measures will not lead to sustainable growth for industries and businesses.
It is necessary to be in close contact with a local region in order to get to know its particular environment and characteristics, and then to envision the best future for that area. Close contact will ultimately lead to the establishment of strong roots and a trusted presence in the community, and among clients.
While anticipating future needs together, Maruyo Seafoods Co., Ltd., and Mayekawa have worked cooperatively to provide value to society. Going forward, Mayekawa will continue to work from this value-creation perspective in order to contribute to a rich and prosperous future.
We're ready to help, wherever you are
Our mission is to create a sustainable future by pursuing optimal systems,
equipment and technology while working
side-by-side with customers.